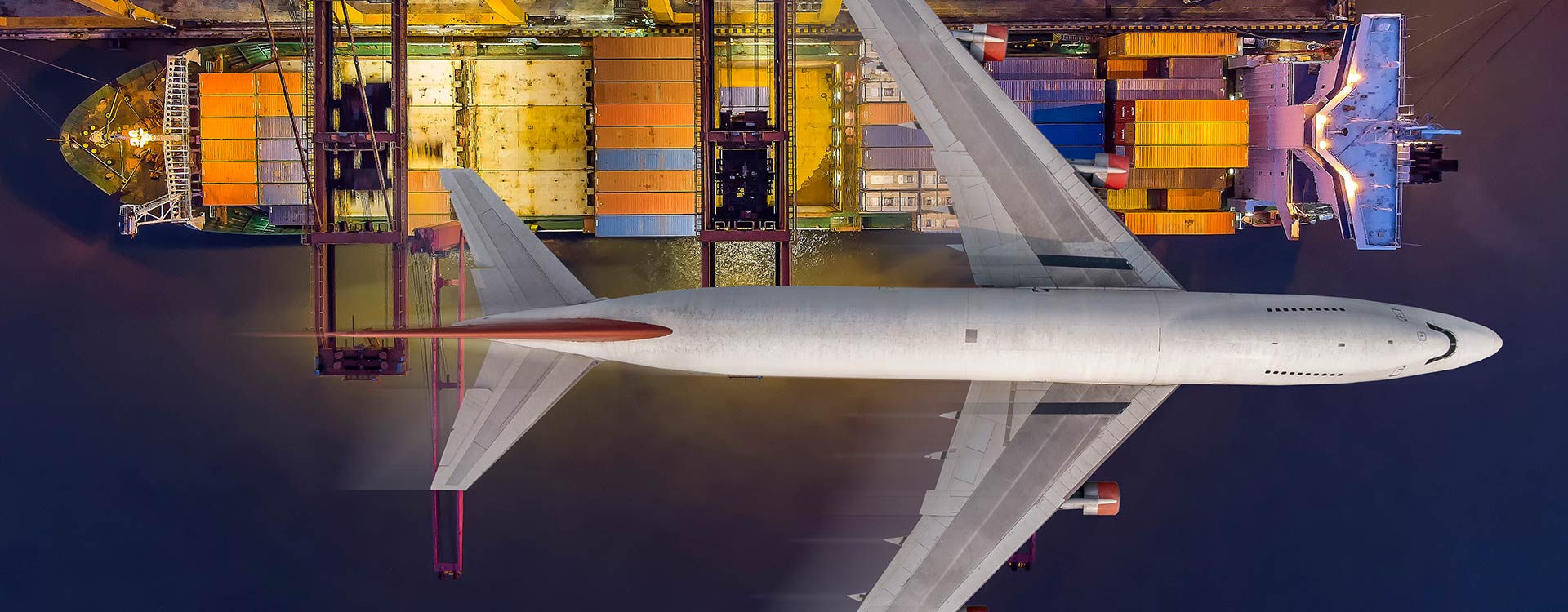
Expect a narrow window of opportunity when the air cargo industry rebounds from the coronavirus downturn. It will be a short period where the carriers most prepared for the return of traditional volumes can significantly out compete the unready. What will your “ready” look like?
If attics, garages and closets recently got overhauled like never before, you know what we are saying here. The positive aspect of the shutdown is the opportunity to take care of matters that make work and life better when it ends. You don’t want to go through so much turmoil and hardship without coming out better for it.
Lockdowns are tentatively lifting now and shuttered industries are slowly recovering, with air cargo poised to be among the first to recover. With decreased capacities limiting cargo opportunities, it is a perfect time to consider preparing the warehouse and employees for the eventual return of “normal.”
What kinds of preparations? Start with asking yourself and your team a few questions:
1. In normal circumstances, what obligatory activities compromise productivity?
Mandatory employee training pulls people away from regular duties. Can some take that training now so that they can hit the ground running when business comes back? Peak productivity requires employee availability instead of tied up with required training.
Stations all have audits in the future – corporate, FAA, TSA and more. These disruptions can throw the rhythm off and pull people from regular duties. Using the downtime now to conduct internal audits, assemble the required information and identify any possible shortcomings as well as apply fixes puts the station ahead of the target. The station will be clean and ready when the official auditors show up – alleviating any worries about the outcome.
2. What chokepoints would a Lean exercise reveal?
Resources may be tight so conducting a whole Six Sigma Lean exercise may be impossible. However, is there time to focus on the most egregious inefficiencies and find solutions? Do a walkthrough of the station workflow and note where significant chokepoints occur – often because “that’s the way they’ve always been.” There are bound to be things that are easy to alter now that business is slower. Start simple! Is the label printer adjacent to the incoming freight? Is sensitive equipment away from dust-raising functions? Do any barriers exist that keep employees from having “eyes on” activities that make a difference in their work? Count steps for various functions – can steps be reduced?
3. Now that the warehouse is slower, how about a spring (summer) cleaning?
Many used the lockdown and extra time at home to finally get rid of boxes of old bank statements, floppy disks holding who knows what and 20 years of tax returns. People tend to hold on to things “just in case” but when “case” never comes, useless things accumulate.
Does your warehouse contain proof of that tendency? What is being held onto in the warehouse? Manuals you no longer use or are outdated (and thus a potential audit issue)? Labels and forms obsoleted by new processes or regulations? Training and process manuals easily accessed online? Replaced equipment and devices but held on to for “just in case?”
While getting rid of those useless things, be thinking about how employees can better use the space. Especially bear in mind that extra space means easier distancing to keep them safe.
4. Any equipment maintenance you had to put off when business was busy?
The best farmers do not spend the winter reading and watching TV. They spend it maintaining their machinery so that on the very first day of planting season, they are out planting without any worries except the weather. That is a good lesson – return from the downturn with all the equipment in perfect working order. Make the rounds – verify the next calibration, thorough cleaning or maintenance cycles. Can it be done now?
For a business trying to make a profit, delays due to equipment breakdowns and inaccessibility are downfalls. Scales, screening equipment, ULDs, nets, straps – make all needed repairs now and watch the effort pay off.
5. What space configuration changes will you have to make – not just for social distancing but also for likely changes in your cargo?
Stations may be required to adopt some form of reconfiguring of space to accommodate distancing regulations. Dictated by the local government’s rules, the requirements of your business processes, the kind of business that comes back and employees’ willingness, the best configuration may be uncertain. Start now to design and prepare for several options.
Keep in mind that the nature of your cargo loads might change significantly. COVID-19 has sparked geopolitical issues with major implications for trade, changing who is shipping what and where. What pent-up demand is likely to explode and require more space than ever before? What will there be less of, now that demand is depressed because of unemployment, bankruptcies, and other financial difficulties? Will you be shipping more cargo with heightened requirements, like fresh food, live animals and drugs?
Engage the entire team – front line, station leadership, sales – in this process. Some may have already come up with great tactics for the new environment. Run options by your engineers for review of process efficiencies. Do your Lean exercise again to ensure that your optional configurations still meet your business process needs. Are you utilizing Digi-Analytics to help see trends and changes? If not, it is a good time to talk to Unisys to find out the data analytic capabilities they can provide.
Is new signage in the stations required? To inform both customers and employees, signage can set the rules of engagement when it comes to distancing and keeping everyone safe. Putting orders in now ensures priority from the print shop.
6. What changes would customers most like to see?
Customers will be looking for proactive communications about your safety measures relative to the virus. How is distancing enabled? What are the masking requirements? Cleaning and sanitizing protocols?
But now that you have the time, what else have they been asking for that you now have time to create? Better yet, reach out and ask them what they would like from you, now that conditions have altered so drastically.
7. And last, but obviously not least, what new expectations do you have of your vendors.
Current changes in the industry may require adaptation and different tools. Vendors like Unisys provide a wide scope of features and functionalities; some you may already utilize, others that you may not. Are you taking full advantage of all that they can provide? Instead of reinventing a new process or creating a new report, your vendor may already have these tools available for you.
If not, what do you need to be better prepared for the future? Your vendors are part of the team. Reach out to explore the possibilities! Working together, weathering this downturn and preparing for the future can ensure the success for every team member, every business, every customer and our communities.
You are coming out on the bright side of a tunnel no one knew was there. Not knowing exactly what form the recovery will take, you only know that you must be, like athletes in every sport, on your toes, knees bent for whatever direction the ball goes. These preparatory activities can ensure that the recovery will find you better prepared than ever to meet your clients’ needs and ready to compete for their business.